Additive Manufacturing – A Unique Opportunity For AI
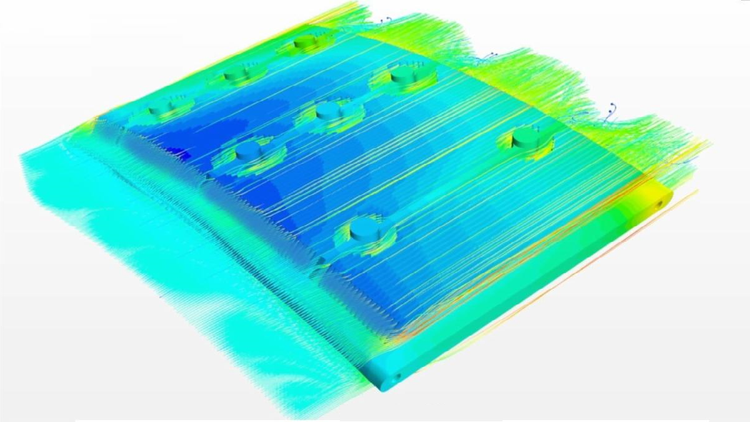
The discussion about whether AI should be used in some aspects of human activities still continues. However, machine learning is already providing significant benefits in design engineering and advanced manufacturing for fields like aerospace, medical devices, and even 3D-printing systems.

Robin Tuluie wrote this piece concerning PhysicsX. It consists of a team of Ph.D. holders who have extensive knowledge in designing Formula 1 racecars. Currently, they are utilizing their skills in 3D printing.
This isn't Design for Additive Manufacturing (DFAM) but rather a type of computerized, AI-directed optimization that delivers ultra-precise, customized, and checked design options for 3D printing.
Changing how products are made globally The process of manufacturing items has come a long way over the years. With the advancements in technology, it is no longer the same as it used to be. The traditional way of production had major challenges, including ineffective procedures and a slow process. But today, technology has transformed the way products are made around the world, and it continues to evolve. Various manufacturing industries are introducing innovative machinery and production processes that enhance efficiency, speed and accuracy. The aim of these new methods is to increase profitability and reduce costs, and, at the same time, minimize waste. As technology advances, the production of better quality and affordable products becomes a possibility. Manufacturers are now able to produce more with less, using fewer resources. They can, therefore, adopt sustainable practices, consume less energy, water, and materials, and reduce their carbon emissions. All in all, technological advancements in production processes have brought about many excellent benefits. They make it possible to transform how the world makes its products and create healthier, more sustainable ways of production.
The digital design and engineering sector, which is the basis of advanced manufacturing innovation, can be improved by AI's profound learning abilities. This has the capability to revolutionize the manufacturing of products in a highly beneficial manner.
Currently, we have a pressing chance to make the most out of the various computer-aided engineering tools (such as CFD, FEA, electromagnetic simulation, and more) by utilizing AI. Specifically, we're referring to design optimization, which is being taken to new heights through the automation of machine learning. This type of optimization is lightning-fast and incredibly accurate, far surpassing what many manufacturers are currently capable of achieving.
The use of AI tools brings about a significant improvement in efficiency and precision. They are capable of reducing simulation times from hours to seconds, and make use of deep learning to evaluate and tweak the geometry of a part based on user-defined limits. This process makes it possible to achieve desired outcomes such as reducing weight, lowering stress and fatigue, improving fluid flow, heat exchange, conductivity, durability, and consolidating parts. The end result is a final design that perfectly combines the desired attributes prioritized by its makers.
How can this be achieved? By reducing the amount of calculations, not increasing it.
The laws of physics are something that cannot be avoided. It is important to do your due diligence when designing, using the best CAE tools that are suitable for your company's product needs. Nevertheless, AI software can enhance the digital-design platform by integrating with your current simulation tools. This helps reduce the amount of calculations needed for each differential equation.
AI achieves this impressive feat by taking a different approach to solving the complex CFD and FEA equations. Using machine learning, it analyzes and mimics the overall physical behavior of a design, rather than delving into each individual mathematical problem that contributes to that behavior. This method is highly efficient, requiring far fewer computational resources, while still providing a thorough evaluation of the design in a variety of environments. In a single day, hundreds of thousands of design options can be tested and assessed. The result? AI has the potential to significantly improve performance, by up to 30% or more, compared to traditional simulation tools. It's important to note, however, that real-world testing of finished parts is still necessary to verify quality and performance standards.
The combination of artificial intelligence (AI) and additive manufacturing (AM) is a dynamic force that can revolutionize multiple industries. The utilization of AI in AM allows for smarter, faster, and more accurate production processes, which has the potential to reduce wastage and increase efficiency. Furthermore, AI can be used to analyze data and create customized designs, making AM a versatile and adaptive technology. By combining these two technologies, manufacturers can work more effectively, cutting down on production times, minimizing costs, and allowing for greater flexibility. The benefits of using AI in AM extend beyond this, with the ability to create more complex and intricate designs than would be possible by humans alone. This union of technologies has the potential to create new business models and products, unlocking new markets and opportunities. In conclusion, the synergy between AI and AM is a powerful toolset for manufacturers and businesses alike. The growth of these technologies in recent years indicates that their potential is only just starting to be realized. As they continue to evolve, the impact of AI and AM combined will become increasingly significant across a wide range of industries.

Although machine learning has the potential to be useful in designing products using any manufacturing process or technology, it is particularly effective in combination with additive manufacturing (AM). With the help of machine learning, the AM-design space can be fully investigated, allowing for the identification of the restrictions of particular components in accordance with the laws of physics. This liberates the unique potential of AM, which can provide incredibly intricate geometric designs that result in the most imaginative and economical solutions to complex engineering problems.
The blend of additive manufacturing and AI has been effectively utilized to enhance and boost the effectiveness of distinct items produced by additive manufacturing. This includes a 3D-printed heat exchanger employed in jet engines, a title-holding motorbike, the impeller blades of a cardiac pump catering to patients experiencing heart failure, and numerous other implementations in technologically progressive industries.
Furthermore, some manufacturers of AM-systems have acknowledged the significance of this proficiency in enhancing their own machines. This leads to saving time, improving efficiency, and refining the precision of their prints.
This is a fascinating case of an AM machinery supplier who utilized deep-learning software to improve the performance of their 3D printer.
With the development of cutting-edge metal 3D printing technology, it is now possible to create components for rockets, airplanes, and heavy industry applications such as oil and gas and power plants. As a result, there has been a significant increase in demand for 3D printers with the ability to produce larger quantities of these high-quality parts. Velo3D, a California-based company, recognized this trend and started developing its Sapphire XC machine with a much larger build chamber, offering a 400% increase in capacity. Additionally, the Sapphire XC incorporates eight 1,000-watt lasers, four times as many as its predecessor, the original Sapphire.
When metal powder material in an AM build chamber is melted using lasers, it creates soot. This occurs because some of the material turns into vapor and then transforms into tiny particles that can clog up the lasers as they work on the powder bed. The remedy to this issue is to have a continuous supply of inert gas (usually Argon, but it changes based on how reactive the melted material is) that can remove the soot as it forms.
At times, particles may break away from the flow and end up sticking to the windows that the laser beam goes through to get into the chamber. This can result in contamination and overheating, which could even damage the window. Consequently, an unintended optical lens is created, which bends the laser light, moving it off its intended course and causing it to lose focus on the material bed. This, of course, negatively impacts the quality of the build. Therefore, it's crucial to keep the laser windows free of dirt throughout the process.
Overcoming the Difficulty of Expanding The task of increasing in size and scope can present obstacles. However, there are ways to conquer this challenge. By identifying areas for improvement and strategically planning for growth, it is possible to successfully expand. It may also require bringing in new talent, seeking out partnerships, or investing in new technology. It is important to approach this challenge with a positive and proactive mindset to ensure success. With determination and hard work, going bigger can be achieved.
Velo3D had previously considered the ideal gas flow for the larger build chambers in their machines. However, the XC system presented a challenge due to its longer powder bed, larger interior volume, and a higher number of tightly packed lasers. Therefore, creating optical window nozzles for the XC system required additional effort. The company predicted that the new machines would generate approximately four times more soot compared to the older models.
At first, the company attempted to conduct computational fluid dynamics (CFD) simulations themselves, but then sought assistance from a software provider. However, the outcomes did not meet their desired standards. The process of configuring numerous CFD simulations and modifying factors such as the nozzle holes' sizes was a challenging task and required a significant amount of time, effort, and guesswork.
Velo3D asked PhysicsX to come up with a solution using their expertise in simulation, optimization, and designing. PhysicsX has extensive experience in these areas due to their involvement in F1 racing, knowledge of data science, machine learning, and engineering simulations. They also have a set of proprietary simulation-validated tools that can automatically iterate designs using machine learning and AI-based simulations. To achieve the desired results, PhysicsX creates a loop involving CFD, generative geometry creation tools, and an AI controller that trains a geometric deep learning surrogate. This surrogate can produce high-quality CFD results in less than a second, which is then used in a super-fast geometrical generative method in another machine learning loop. The result is a design that optimizes based on multiple objectives determined by the engineer using highly accurate deep learning tools and a robust workflow. The final product undergoes validation against a CFD model to ensure its accuracy, thanks to the fidelity of the deep learning tools used by PhysicsX.
The Velo3D team used various measurements to determine how much of the recirculating flow was moving upward toward the window in the nozzle. PhysicsX assessed the Sapphire window proposal when the project began, and then utilized their unique artificial intelligence/machine-learning software to conduct extensive simulations to fine-tune the final design. The outcome was a nozzle that produced an ideal flow of Argon curtain while still operating within the additive machine's manufacturing capacity.
The complexity of the last turning-vane layout may pose difficulties for regular additive manufacturing processes, however, the Sapphire device's capacity to print very narrow, smooth, and shallow-angle vanes produced the precise shape that facilitated the nozzles to work as intended. The ultimate blueprint was fine-tuned for and forged on the initial Sapphire printing machine and the initial Sapphire XC was efficiently operated using the recently installed window-nozzle components – an instance of an additive manufacturing machine generating its individual parts.
A Chance to Enhance Additive Manufacturing Designs Have you ever thought about taking your designs to the next level with additive manufacturing? Now is the perfect time to do so! With endless possibilities for customization and creativity, this technology provides the opportunity for you to transform your designs into something extraordinary. Don't miss out on this chance to enhance your additive manufacturing creations and stand out from the crowd.
The AM-nozzle-optimization instance demonstrates how AI design optimization and 3D printing can work together to their fullest potential. Nowadays, no modern technology can come to fruition without the inclusion of computer simulation. However, the simulation process still requires a considerable amount of computing power and human optimization expertise, which can impede progress – something that the AM industry is currently addressing.
AI can play a vital role in enhancing and streamlining decision-making processes for engineers and designers who work with additive technologies. For instance, deep learning optimization can help to modify the design of a functional 3D-printer component, and in the process, improve the performance of the laser system responsible for high precision, leading to better end product quality. These features are what industries such as aerospace, science, medicine, and automotive are searching for to achieve global growth and success. Therefore, deep learning can act as a catalyst that speeds up the progress of the additive manufacturing industry towards accomplishing these objectives.